The company’s expertise in environments with potentially explosive atmospheres has expanded even more
ATAM, a key player in the field of encapsulated coils and industrial connections for process valves and solenoid valves in pneumatic and hydraulic applications, is continuously proving to be a reliable benchmark for the ATEX world. Indeed, the first encapsulated coil with external magnetic armature (called the 481), certified according to ATEX Directive 2014/34/EU, was recently introduced on the market for standard hydraulic applications.
The 481 ATEX-certified coil offered by ATAM can be applied in Zone 2 according to Directive 99/92/EC – where areas at risk of explosion are classified in terms of zones on the basis of the frequency and duration of the occurrence of an explosive atmosphere.
ATAM’s 481 coil has a high protection rating in accordance with IEC-EN 60529 and can be supplied with between 12 V and 240 V direct and alternating current. It is made according to a very complex manufacturing process that involves the complete absence of gaps in which gas can penetrate; it has an internal diameter of 22 mm, an external diameter of 45 mm and a height of 54.5 mm, dimensions that are the most widespread standard in hydraulics.
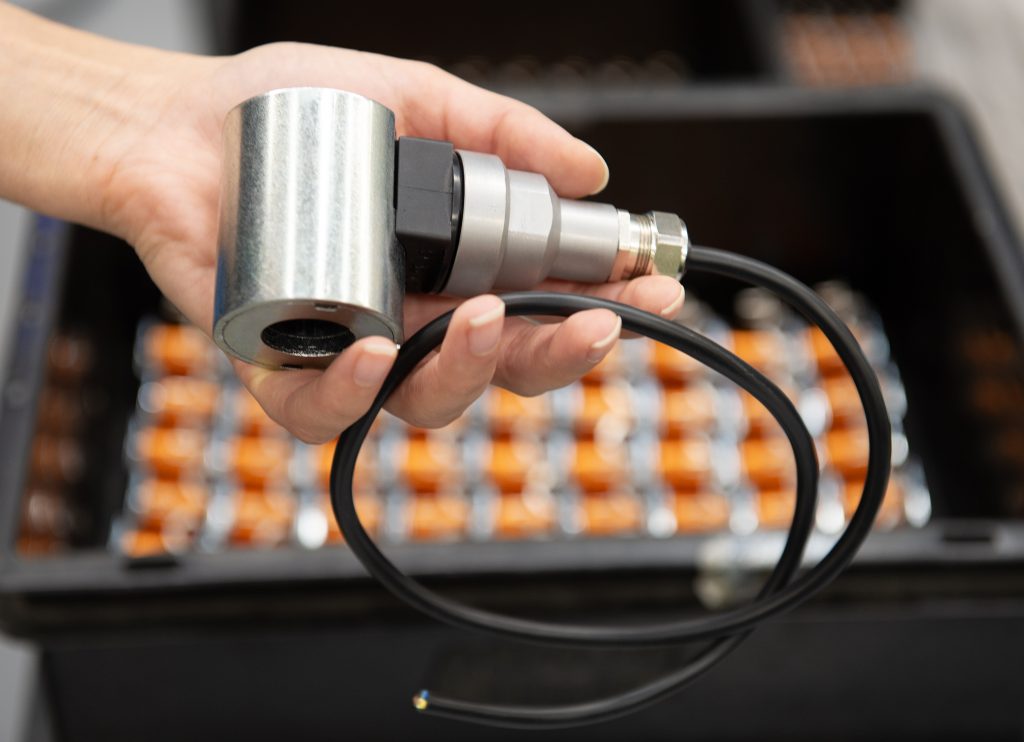
The ATEX certification of the 481 coil gives users the peace of mind of being able to use a coil with an encapsulated external magnetic armature and not with an explosion-proof housing, typically used in ATEX hydraulic applications. The latter is, in fact, heavily depotentialised to operate in such areas, resulting in limited capacity and pressure in these environments.
The unique feature of ATAM’s 481 coil of not having to be significantly depotentialised ensures that solenoid valve manufacturers can continue to use standard products in potentially explosive atmospheres without having to create new valve bodies, in full compliance with the regulations in force, guaranteeing all safety margins and with a substantial cost reduction. And all this with the reassurance of ATEX certification by a third party with expertise in the field.
With the ATEX certification of the 481 coil, which follows only a few months after the introduction of Form A and Form B cable connectors, and precedes the release of overmoulded connectors, which are also ATEX-certified, ATAM further expands its expertise in potentially explosive environments with products – connector + coil – that benefit from joint development. This is thanks to in-house personnel highly specialised in this still quite unknown field and a state-of-the-art experimental laboratory that allows the company to simulate the combined use of the two products and verify the tightness of components even under heavy duty requirements. This results in excellent solutions in terms of reliability, quality and affordability.
There are far more environments with potentially explosive atmospheres than one might expect. Apart from the oil industry and mining, in fact, there are many environments that require an ATEX approach due to the presence of gases, vapours and dust that can create explosive atmospheres in the vicinity of an ignition source (e.g. hot surfaces, electrical material, electrostatic charges, mechanical sparks, etc.). Basically, about 70% of industrial environments are susceptible to this type of risk.
More than 30 years of competence
For over 30 years now, ATAM has been on a mission to deal with the ATEX world with increasing competence, offering connectors and different families of coils over time, including custom-made ones, for the most common pneumatic and hydraulic applications, covering the various ATEX risk categories.